Restore Rubber Feed Rollers in Thickness Planer
Causes of planer snipe on small thickness planers
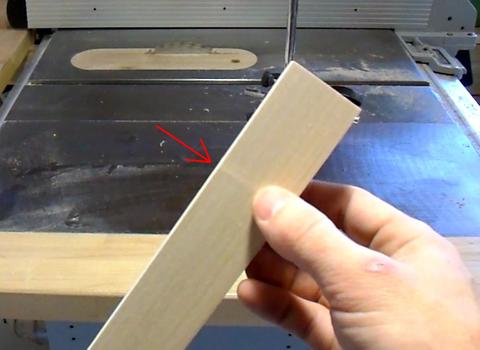
For small thickness planers, snipe is primarily caused by movement of the cutter head assembly. I constructed a simple wooden model to illustrate what happens.
As the board exits the planer, the infeed roller runs off the end of the board. The rubber rollers apply quite a bit of downward pressure to the board, and as the roller rolls off the board, there is a lot less upward pressure against the head assembly from the roller, so the whole head assembly typically moves down a tiny bit.
The same thing happens at the start of the board when the board starts to engage the outfeed roller.
On my old Delta thickness planer, this snipe is on the order of 0.008" (0.2 mm). Fortunately, the rollers are very close to the cutter head, so only the first and last 5 cm of the board are affected.
This type of snipe can be avoided by feeding boards behind each other so that they touch and the roller never rolls off the boards (see here), although it can be hectic keeping the planer fed while picking up the pieces coming out of it at the same time.
Some of the better small thickness planers have a head locking mechanism. This locks the planer head to the columns that it rises up and down against. Other planers have four screw-columns to move the head up and down. Both approaches greatly reduce head movement and corresponding snipe.
My old delta planer doesn't have a head lock and it only has two screw columns, but it occurred to me that if I were to insert spacers between the planer head and the table and press the head down against those spacers, that might have the same effect.
But placing individual blocks would be awkward. So I made some "spacer bars" to stick into the planer. These have a thin part in the middle so that the rollers and planer head won't touch my spacer.
The spacer bars are only good for one thickness, but I figure if I had to repeatedly plane boards of the same thickness, this could actually be a useful feature.
With the spacer bars clamped in, I measured about 0.002" of snipe on one end, and no detectable snipe on the other end.
Another cause of snipe can be if long boards are fed into the planer unsupported. this will cause the board to tilt up a little and get close to the cutter head at the beginning and end of the board.
The rubber infeed and outfeed rollers are spring loaded and only press down so hard, so they won't prevent the board from tilting up a little bit.
You can avoid this type of snipe by making sure the board doesn't sag down going in and coming out of the planer. A longer table, or folding tables on the jointer also prevent this type of snipe.
Most small thickness planers nowadays come with fold-down infeed and outfeed tables, which largely prevent this type of snipe from happening. My old Delta planer came with two sheet metal tables that could be hooked to the planer, but they were kind of ugly and need to be placed on a large level surface. So I never actually used them. This cheap MasterCraft planer (store brand from Canadian Tire) comes with fold down infeed and outfeed tables.
I got this planer on sale for just $200, half as much as I paid for my old Delta planer back around 1998. As far as I can tell, it's a better planer than the Delta. Part of the reason I bought it was so I could disassemble it to for the cutter head which I used to build a 12" jointer. But with this being a better planer than my old Delta planer, I disassembled the Delta planer instead.
For large cast iron planers, typically, the head is fixed in place and the table moves up and down. This means the head won't move, but sometimes the table will move or flex because of the varying amounts of downward pressure applied by the feed rollers.
Some large thickness planers have rollers in the table. This makes the boards less likely to get stuck, but the rollers in the bed can also be a source of snipe. Worse yet, when planing softwoods, sometimes the rollers get gummed up with pine tar, which will later mark up the board, or cause a sort of periodic snipe as the bumps on the rollers push the board up. So rollers in the table are not always a good idea.
See also:
Source: https://woodgears.ca/jointer/planer_snipe.html
0 Response to "Restore Rubber Feed Rollers in Thickness Planer"
Post a Comment